Aluminum Anodizing: Technology, Advantages, and Disadvantages
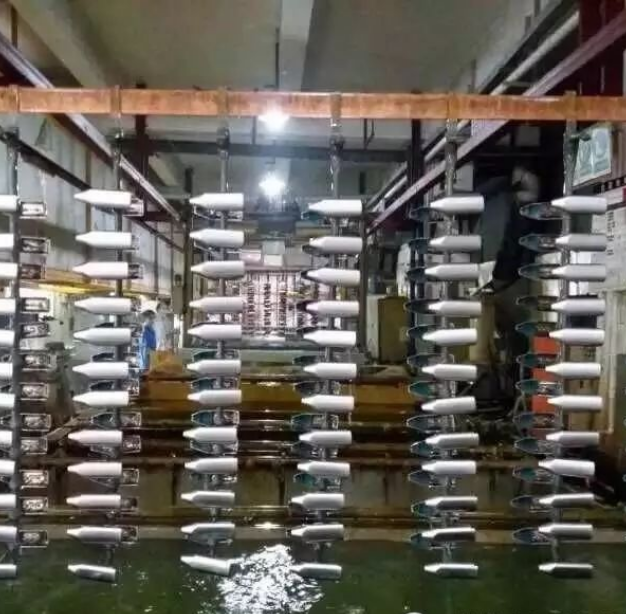
Aluminum anodizing is a common surface treatment process that enhances the corrosion resistance, aesthetics, and functionality of aluminum by creating a durable oxide layer on its surface through electrochemical means. This article provides a clear and concise overview of aluminum anodizing, including its definition, working principles, applications, types, advantages, disadvantages, and practical considerations.
What is Aluminum Anodizing?
Aluminum anodizing is an electrochemical process that forms a protective aluminum oxide (Al₂O₃) layer on the surface of aluminum and its alloys. The anodized layer significantly improves corrosion resistance, wear resistance, and aesthetic appeal, making anodizing an essential technique in aluminum processing and application.
Applications of Anodized Aluminum
Anodized aluminum is highly valued across various industries for its exceptional corrosion resistance, hardness, wear resistance, and decorative qualities. Key application areas include:
With its versatile functionality and aesthetic appeal, anodized aluminum is indispensable in industries ranging from aerospace to consumer goods. As technology advances, its properties and application potential will only expand.
How Does Aluminum Anodizing Work?
Anodizing uses an electrochemical reaction to form a controlled oxide layer on aluminum by immersing it in an acidic electrolyte and applying an electric current. Unlike paint or plating, the anodized layer integrates with the aluminum substrate, making it highly durable.
1. Fundamental Electrochemical Reactions
When current is applied, oxygen ions (O²⁻) in the electrolyte migrate to the aluminum surface and react with aluminum atoms:
2Al+3O2−→Al2O3+6e−2Al + 3O^{2-} \rightarrow Al_2O_3 + 6e^-2Al+3O2−→Al2O3+6e−
This reaction generates an aluminum oxide layer on the surface and releases electrons to sustain the electric current.
2. Dual-Layer Structure of the Oxide Film
The anodized film consists of two distinct layers:
3. Role of Current and Voltage
4. Post-Treatment Processes
After anodization, additional treatments are often applied:
Key Factors Influencing Anodizing
Advantages of Aluminum Anodizing
Improved Corrosion Resistance:
The oxide film prevents aluminum from reacting with oxygen, moisture, or acidic substances.
Applications: Ideal for humid or industrial environments, such as curtain walls, frames, and marine structures.
Enhanced Hardness and Wear Resistance:
Hard anodizing forms a highly durable layer, reducing scratches and abrasion.
Applications: Industrial machinery parts, sports equipment, and high-wear components like rails and slides.
Enhanced Aesthetic Appeal:
Offers a variety of finishes, from matte to high gloss, and colors through dyeing.
Applications: Consumer electronics, home decor, and architectural elements.
Increased Adhesion:
The porous structure enhances paint, coating, and adhesive bonding.
Applications: Coated aluminum products, composites, and aerospace parts.
Better High-Temperature Performance:
Anodized layers resist oxidation or softening at moderate temperatures.
Applications: Heat exchangers and industrial tools.
Improved Electrical Insulation:
The oxide layer acts as an insulator for electrical applications.
Applications: Electrical housings and components.
Environmental Friendliness:
Anodized coatings contain no organic solvents, making them eco-friendly.
Applications: Green building materials and consumer goods.
Extended Lifespan and Low Maintenance:
Anodized aluminum requires minimal upkeep, reducing overall costs.
Applications: Long-lasting construction materials and outdoor furniture.
Disadvantages of Aluminum Anodizing
Higher Processing Costs:
Specialized equipment, materials, and energy increase costs, particularly for hard or colored anodizing.
Susceptibility to Impact Damage:
The anodized layer, though hard, is brittle and may crack or chip under heavy impact.
Limited Corrosion Resistance in Harsh Environments:
Strong acids, alkalis, or chloride-rich environments can degrade the oxide layer.
Non-Repairable Coating:
Damaged oxide layers cannot be easily repaired and often require re-anodizing.
Color Limitations:
Dyeing options are constrained, especially for hard anodizing, which typically results in gray or black finishes.
Uneven Coating on Complex Shapes:
Sharp edges or recessed areas may experience uneven film thickness.
Reduced Conductivity:
The oxide layer is an insulator, which can be a disadvantage for electrical applications.
Dimensional Changes:
The anodized film increases part dimensions slightly, which may affect precision in tight-tolerance applications.
Environmental Concerns:
Electrolytes like sulfuric acid and chromic acid require proper waste treatment to prevent pollution.
Conclusion
Aluminum anodizing is a versatile and effective process that combines functionality and aesthetics. By selecting the appropriate type and parameters, anodizing can maximize performance and cost-effectiveness in diverse applications. However, careful consideration of its limitations is essential to ensure it meets specific requirements.
- Art
- Causes
- Crafts
- Dance
- Drinks
- Film
- Fitness
- Food
- Jocuri
- Gardening
- Health
- Home
- Literature
- Music
- Networking
- Alte
- Party
- Religion
- Shopping
- Sports
- Theater
- Wellness